A Pulley Lagging for every Application
Belt Conveyor Drum lagging
The role of a conveyor pulley lagging depends on its function on the conveyor, its field of application, and external conditions.
Drum Pulley lagging can be used to increase adhesion and the coefficient of friction with the conveyor belt. It also serves as a wear layer to protect the conveyor pulley and reduces the risk of slippage, ensuring the conveyor operates efficiently. This rubber lagging, also referred to as lining, is a key element in optimizing conveyor system performance.
At ALTEMA, we offer lagging solutions tailored to all types of drums, whether it’s drive pulleys, where optimal adhesion is essential to ensure efficient power transmission, or tension drum pulleys, which may require specific lagging to prevent excessive slippage, particularly in applications demanding precise belt tension.
We are capable of lagging drums and pulleys in our workshops with rubber or ceramic coatings of various thicknesses and hardness levels. Different types of lagging are available to address the specific constraints related to the drum’s position on the conveyor, the material being transported, or the operating environment:
- ceramic lagging
- rubber lagging
- diamond lagging
- Anti-Caking
- anti-abrasion
- food-grade (FDA white or EU1935/2004)
- anti-grease or ISO 284 / 340.
Drum pulley rubber lagging can be applied through cold bonding or hot vulcanization processes, depending on the technical requirements of the application.
Need for
Technical advice?
Call our drum experts
Profile types
Diamond
The universal lagging
Used on deflection and take up pulley. It is also suitable for head pulley.
Ceramics
The high-adhesion lagging
Effective in humid environments to prevent slipping on the conveyor belt.
Smooth
Protective lagging
For conveyor pulleys that don’t drive the belt, to extend their service life.
Pulley bars
Anti-skid lagging for large drums
Ruggedly designed, the anti-skid bars are made of wear-resistant rubber for long life.
Griplag
For tough conditions
The Griplag prevents slippage and is self-cleaning, preventing material build-up and misalignment.
The benefits of rubber lagging
- Bonding systems (used for applying rubber lagging) that are easy, quick, and tailored to your needs.
- The lagging protect the belt and significantly improve the conveyor’s overall performance, thus extending its service life.
- They ensure that rollers and drum pulleys rotate smoothly without clogging, thus maintaining and aligning the conveyor belt.
- Rubber lagging on a drum or pulley protects the belt by reducing slippage between the belt and the drums.
- They reduce conveyor noise and vibration.
A range of drum pulleys for all sectors of activity
ALTEMA's experience enables us to meet both classic conveyor pulley and handling drum pulley requirements, as well as more specific needs in all sectors of activity: mining, quarrying, recycling, fertilizers, ports, food processing.
+10,000 Drum pulleys per year
+10 Business sectors
+500 satisfied customers
VARIOUS LAGGING AND PREPARATIONS
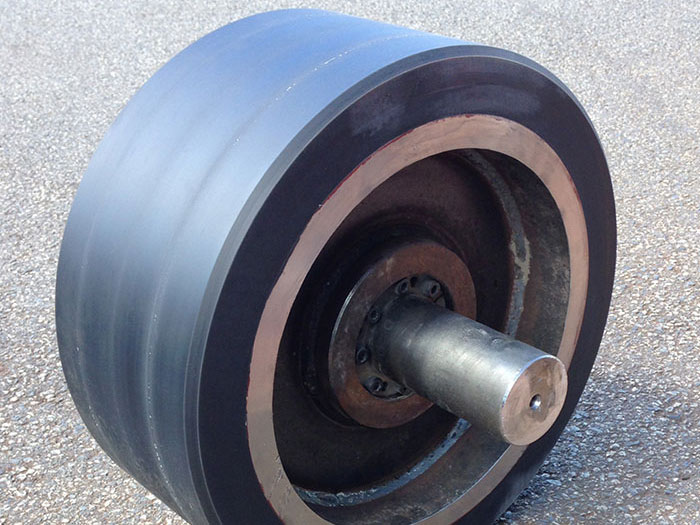
Hot vulcanization
Vulcanisation is a chemical process that gives the drum pulley lagging greater tensile strength, swelling, abrasion resistance and elasticity.
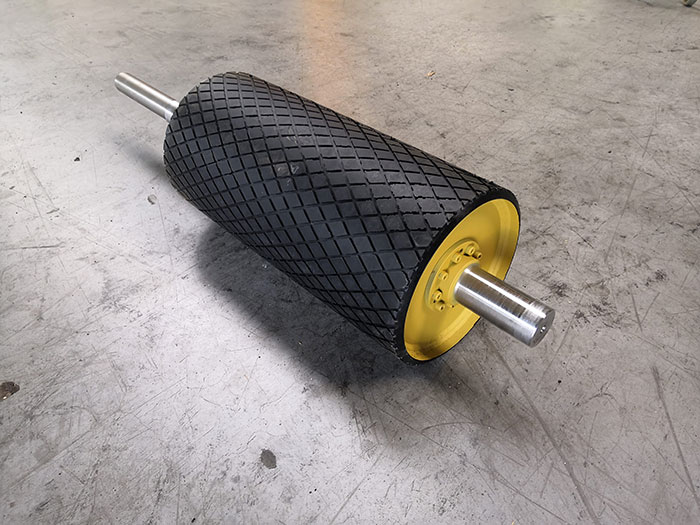
Cold rubberising
Cold rubber bonding is generally used on "classic" drum pulleys for rubber coatings with smooth, diamond-shaped ceramic inserts.
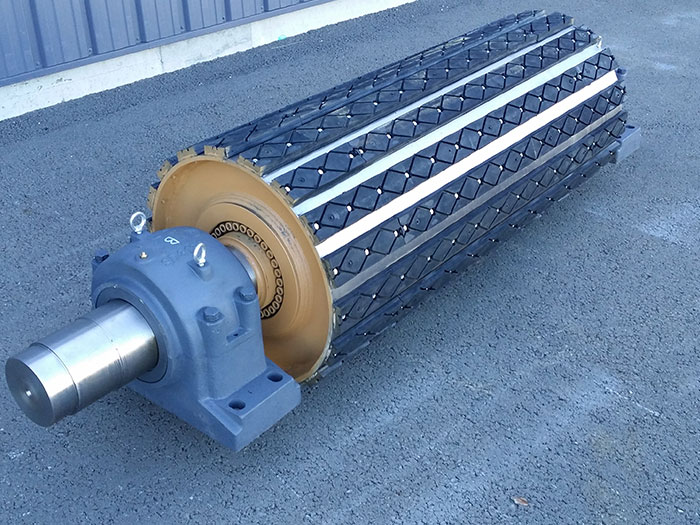
Special rubberizing
Coatings such as Slide Lag, Pulleybars or Griplag are applied to conveyor drums and conveyor pulleys by mechanical assembly.
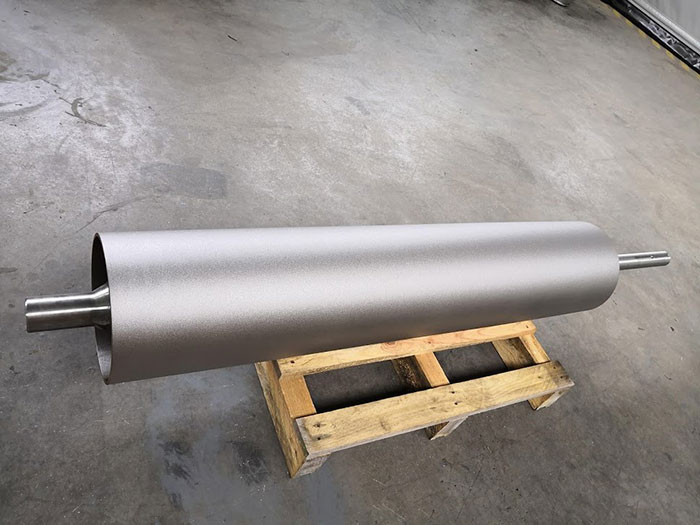
Shot-blasting
All coated conveyor pulleys are shot-blasted for improved surface preparation. This preliminary work is essential for optimum adhesion to the conveyor belt pulley.
Technical Support in Defining Your Products
With over 25 years of experience and expertise in manufacturing custom and specialized belt conveyor pulleys (such as wing pulleys, self cleaning pulleys, etc.) for industries like food processing, mining, and quarrying, ALTEMA supports its clients in the technical definition of their belt conveyor belt drums and pulleys, particularly in selecting the most suitable lagging. The aim is to provide the technical function with the longest service life, while ensuring the best value for money on the market.
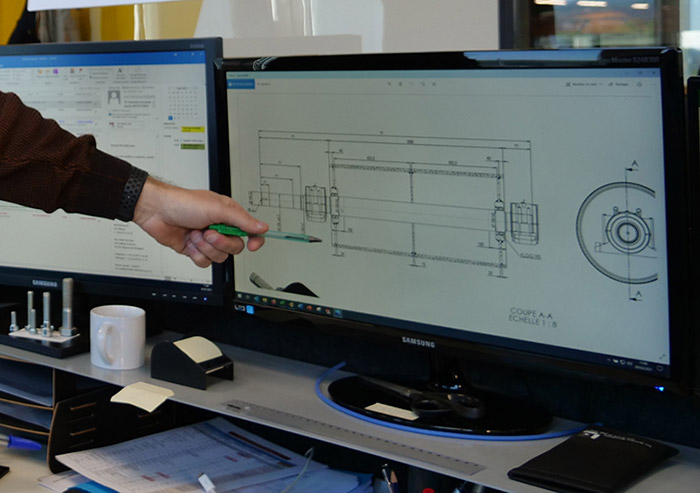
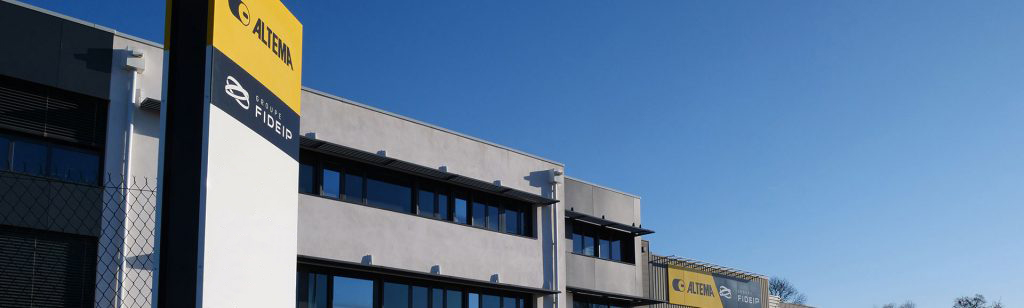
Altema services
RDM DIMENSIONING
ALTEMA's Engineering Department is able to dimension and verify conveyor drum pulleys and elevator pulleys using its RDM and 3D CAD calculation software.
Static and Dynamic Balancing
ALTEMA offers balancing solutions and services for high-speed conveyor pulleys, to keep them running at peak performance.
TECHNICAL SUPPORT
Depending on the application, the field of activity, the transported material and the climatic conditions, ALTEMA offers you specific solutions to optimise your products and improve your performance.